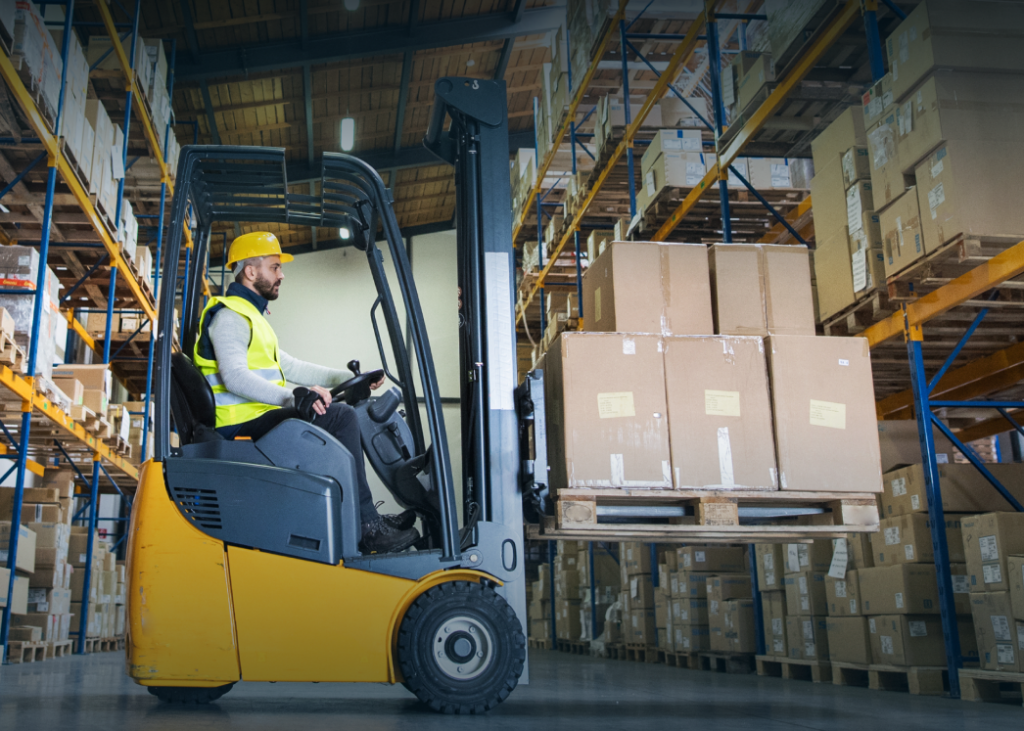
Tips To Ensure Adoption Of Digital Safety Inspections
Implementing a digital solution for equipment safety is a significant step toward enhancing workplace safety, improving OSHA and DOT compliance, and reducing risks. A recent survey of frontline workers in manufacturing and warehouse jobs cited in Safety + Health Magazine showed that over 50% of workers spotted 1-2 safety hazards per week. Both the DOT and OSHA require inspections of vehicles and equipment before use, and they can fine businesses that fail to meet the performance and record-keeping requirements for these safety inspections.
Digital inspection platforms that can automate safety reporting, training and visibility to corrective actions directly address the safety improvements that regulatory agencies require. However, the success of such a system hinges on its adoption by the very individuals who will interact with it daily – frontline operators. If these workers do not embrace the system, its effectiveness is severely compromised, leading to safety gaps and operational inefficiencies. To achieve successful adoption, embracing these best practices is essential:
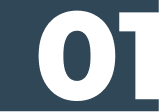
Focus On Usability
A system that is difficult to navigate or requires cumbersome data entry can quickly become a source of frustration for its users. If the interface is not intuitive, operators may struggle to complete tasks efficiently, leading to errors or omissions in safety procedures. If issue reporting is not quick and easy, workers may opt to delay using the digital solution, increasing equipment safety risks. Over time, this frustration can result in a reluctance to use the system at all, undermining the safety protocols it was designed to enforce.
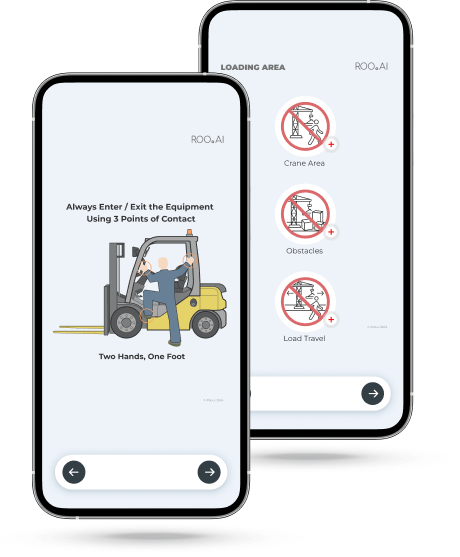
Best Practice: To ensure good usability, prioritize user-friendly design during the selection of the digital inspection technology and the design and implementation of the system. The interface should be clean, simple, and easy to navigate, even for those who may not be tech-savvy. Conduct usability testing with actual frontline workers during the evaluation, design and implementation phases to identify and address any potential issues. Data entry processes should be streamlined with features like drop-down menus, multi-choice or multi-select answers, autofill options, and error-checking prompts to reduce the burden on workers and ensure data accuracy.
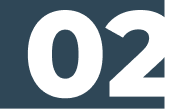
Align Safety With Daily Flow Of Work
When the system does not align with the natural flow of work, it can create bottlenecks and inefficiencies. Operators may feel that the system is an additional burden rather than a tool designed to help them, which will slow adoption. Particularly regarding safety inspections, the workers should not be forced to significantly alter standard processes or disrupt their workflow to capture safety issues or benefit from safety notifications.
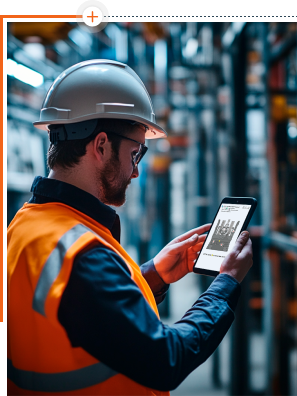
Best Practice: The key is that the digital safety system should be designed to enhance the user’s ability
to perform safety reporting or receive safety notifications without requiring them to deviate significantly from their usual routines. Digitalization can greatly improve accessibility to real time safety reporting as compared to paper, but both process and physical issues should be taken into consideration. Engage with frontline workers during the design and implementation phases to understand their workflows and ensure that the system aligns with their needs. Thought should be given to device access, badge and QR code scanning to simplify access and shorten navigation to appropriate digital safety workflows. Look for technology platforms that make safety data readily available to frontline teams in context and incorporate alerts or notifications…
Continue reading Stephen Zocchi’s ebook to discover other steps to enhance workplace safety.
Download the comprehensive report in PDF format to delve deeper into actionable strategies
for safer work environments.