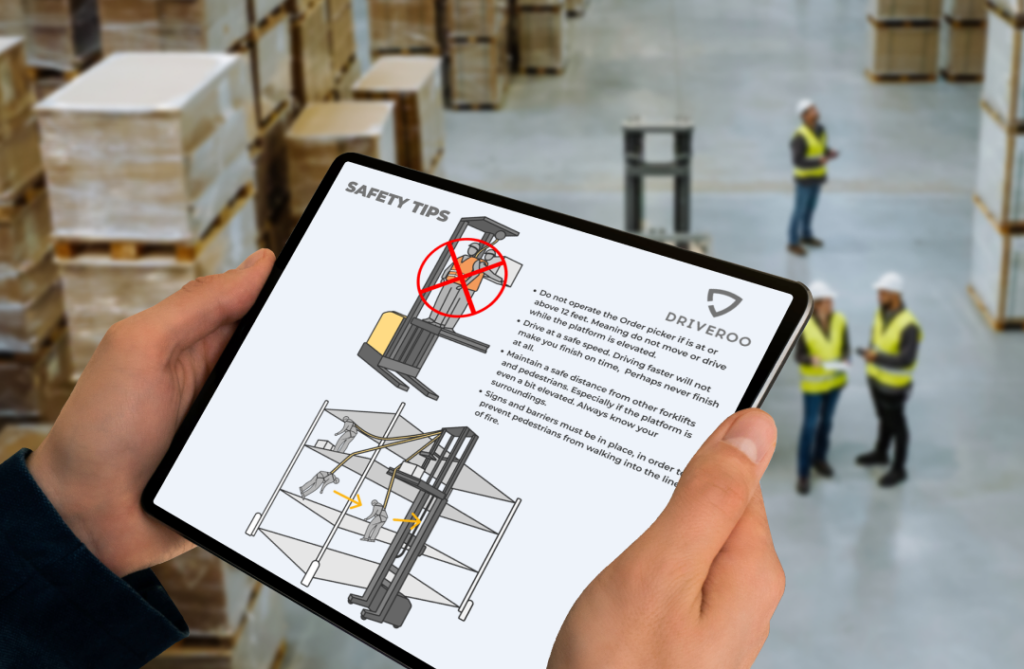
Best Practices To Ensure OSHA Compliance For Power Lift Equipment
Power lift equipment, including forklifts, scissor lifts, and pallet jacks, are an essential part of operations across many industries, from manufacturing to retail. However, improper use can lead to significant safety risks and costly OSHA violations. To ensure compliance with OSHA regulations and maintain workplace safety, employers must be proactive about promoting and enforcing processes and behaviors that increase power lift equipment safety. A focus on the following best practices can significantly improve OSHA compliance.
Rigorous Operator Training and Certification
Training and certification are fundamental to OSHA compliance. All operators must complete a rigorous training program that includes instruction on equipment operation, load capacities, and safety protocols. Provide practical, hands-on exercises that teach maneuvering, loading, and hazard management in real-world scenarios that also address specific company-site hazards, such as uneven surfaces, narrow aisles, or areas with high pedestrian traffic. Ensure operators are evaluated on their ability to safely and effectively use the equipment. Re-certification is required every three years, or sooner if the operator has been involved in an accident, observed operating unsafely, or exposed to significant changes in the workplace.
Daily Pre-operation Inspections
A key to safe, OSHA-compliant operations are daily pre-operation inspections. These inspections, required by OSHA, ensure that equipment is in good working order before each shift. Operators should visually examine parts like forks, tires, chains, and hydraulic systems for damage or wear. Functional tests should confirm that brakes, steering, controls, warning devices, and lights operate correctly. Fluid levels, including fuel, battery fluids, oil, coolant, and hydraulic fluids, must also be checked to ensure they meet manufacturer specifications. Any issues identified during these inspections should be reported immediately, and unsafe equipment should be taken out of service until repairs are made.
Regular Preventive Maintenance
A robust preventive maintenance and repair program is essential for maintaining safe, compliant equipment. In addition to the daily pre-operation inspections, companies should follow the manufacturer’s recommended maintenance schedule for regular inspection and service. Issues identified during pre-operation inspections and preventive maintenance checks should be promptly addressed and repairs must be performed by qualified technicians to ensure they meet safety standards. Detailed maintenance logs should be kept, as they not only demonstrate compliance during OSHA audits but also help identify patterns that may indicate recurring issues.
Proper Load Management
The most common type of lift equipment accident is tip over, resulting in 42% of all power lift equipment fatalities. Proper load management is vital to reducing the risk of these types of accidents. OSHA regulations require operators to avoid exceeding the rated capacity of the equipment. Loads must be secured using straps, clamps, or other methods to prevent shifting or falling, and should be evenly positioned to maintain stability. Operators should never lift loads that block their view, and spotters should assist when visibility is limited. Training should include specific load capacities and configurations to ensure safe handling practices.
A Focus On Safety
Effective safety practices contribute significantly to compliance and overall workplace safety. Companies should clearly mark designated lift equipment lanes and pedestrian zones to minimize potential incidents and near-misses. Speed limits for power lift equipment should be strictly enforced, and unsafe driving behaviors addressed promptly. Work areas should be well-lit, free of clutter, and adequately ventilated to promote safety. Additionally, employees should be equipped with necessary personal protective equipment, such as high-visibility vests and hard hats. Regular safety notices, tool talks and easy access to safety training help reinforce these practices and address potential risks in the workplace.
Thorough Recordkeeping
The backbone of demonstrating OSHA compliance lies in good documentation and recordkeeping. Companies are required to maintain records of operator training and certifications, including the dates, trainer credentials, and scope of instruction. Daily inspection logs should document findings, corrective actions taken, and operator sign-offs. Maintenance and repair records must reflect adherence to recommended schedules and detail how issues were resolved. Incident reports, including accidents and near-misses, should also be diligently maintained. Well-organized documentation not only demonstrates compliance during OSHA audits but also provides insights for improving safety protocols.
Following Best Practices Is Easier Than Ever
Maintaining OSHA compliance for power lift equipment requires a holistic approach that integrates training, daily work procedures, corporate culture and administration. While most companies have relied on paper forms and physical documents, modern digital technologies can now transform power lift equipment safety and OSHA compliance by making the best practices discussed in this article easier, faster and more effective. By digitalizing operator training, thorough daily inspections, proactive maintenance, careful load management, effective safety practices, and meticulous recordkeeping, companies can create a safer working environment, reduce the risk of accidents, and avoid costly penalties. A proactive commitment to safety and compliance is not just a regulatory obligation but a critical responsibility to every worker who operates or works near this essential equipment. Achieving this goal is easier than ever.