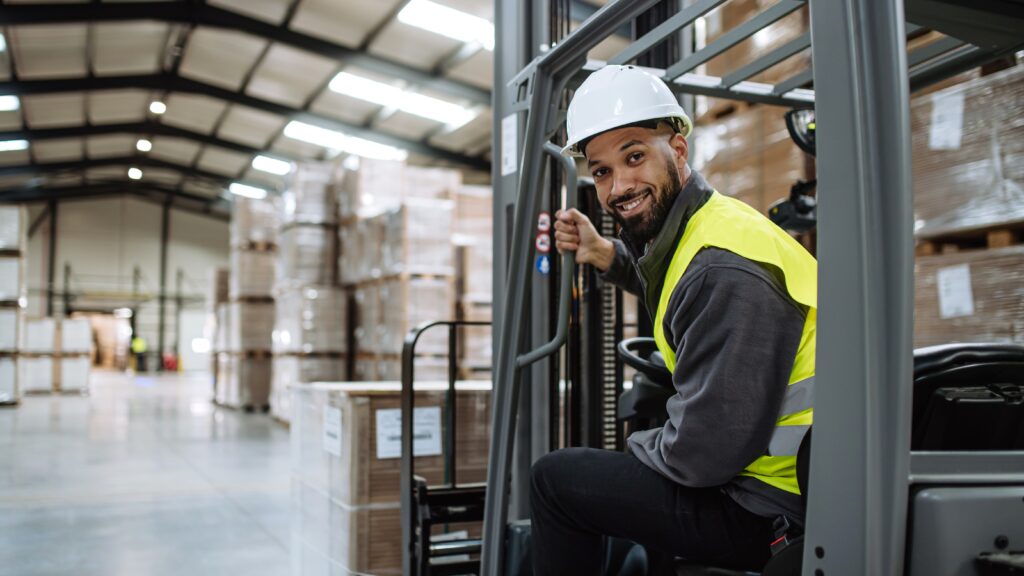
Safety Best Practices for Warehouse Workers Using Power Lift Equipment
Efficiency and productivity are crucial in warehouses. Power lift equipment like forklifts, pallet jacks, and scissor lifts keep operations running smoothly. However, the improper use of these tools can lead to accidents, injuries, or even fatalities.
Prioritizing warehouse safety is not only a regulatory requirement but also a sound business practice that promotes the well-being of the workforce and the business. Following some basic warehouse equipment safety best practices, companies with warehouse operations can ensure their workers optimize both safety and productivity.
Comprehensive Training and Certification
Effective and thorough training is the cornerstone of safe warehouse equipment operation. Workers must receive hands-on instruction tailored to the specific types of equipment they will use. This training should include:
- Basic Operation: Understanding the controls, maneuvering techniques, and braking systems of the warehouse lift equipment.
- Load Management: Recognizing weight limits and proper load balancing techniques.
- Hazard Awareness: Identifying risks such as narrow aisles, inclines, or pedestrian zones.
- Emergency Procedures: Knowing how to handle mechanical failures, power outages, or accidents involving power lift equipment.
Employers must ensure that workers are certified to operate power lift equipment, especially in jurisdictions regulated by agencies such as OSHA (Occupational Safety and Health Administration). Certification should be renewed periodically, and refresher courses should be provided to reinforce knowledge and address evolving industry standards.
Pre-Operational Inspections
Before each shift, forklift operators should conduct a thorough inspection of their lift equipment to identify potential hazards or mechanical issues. A standardized checklist can help ensure consistency and thoroughness. Key inspection points include:
- Tires: Checking for wear, cracks, or proper inflation.
- Fluid Levels: Ensuring adequate levels of oil, coolant, and hydraulic fluid.
- Brakes and Steering: Verifying responsiveness and functionality.
- Forks and Chains: Inspecting for damage or deformation.
- Safety Features: Testing horns, lights, seatbelts, and alarms.
If any issues are identified, workers must report them immediately, and the equipment should be tagged as “Out of Service” until repairs are completed. Attention to equipment condition and regular maintenance minimizes the risk of accidents caused by equipment failure.
Preventive Maintenance of Lift Equipment
Preventative maintenance, in combination with pre-operation inspections, is essential for keeping power lift equipment in safe working condition. Warehouse operators should establish a maintenance schedule that includes routine inspections by mechanics and operator inspections. Regular maintenance services should be scheduled and carried out by qualified technicians. Maintaining a record of preventive services and repairs is also a best practice that can ensure equipment managers have a handle on warehouse lift equipment safety and operating condition.
Wearing Appropriate Personal Protective Equipment (PPE)
Personal Protective Equipment (PPE) is vital for safeguarding warehouse workers from physical injuries. Employers should ensure that all operators and warehouse workers have access to appropriate PPE as may be required for their jobs, including steel-toed footwear, high-visibility vests, hard hats, or protective headwear and gloves. Management should regularly inspect workers’ PPE to ensure they follow appropriate guidelines and that the PPE remains in good condition and fits properly. Training sessions on the correct use of PPE can further enhance its effectiveness.
Adhering to Load Capacity Guidelines
Overloading power lift equipment is a leading cause of accidents, including tip-overs and dropped loads. Operators must always adhere to the equipment’s rated load capacity, which can be found on the equipment manufacturer’s data plate. Some best practices include:
- Load Balancing: Ensuring that weight is evenly distributed to prevent instability.
- Securing Loads: Using straps, shrink wrap, or other securing methods to prevent movement during transit.
- Using Proper Attachments: For unusual or oversized loads, operators should use attachments designed specifically for the task.
Warehouse operators and management should provide clear signage in the warehouse to remind workers of capacity limits and the importance of proper loading techniques.
Operating at Safe Speeds
Speeding is a common but avoidable cause of accidents involving power lift equipment. Operators must adhere to speed limits and adjust their speed based on conditions. During equipment training, speed safety practices should be emphasized such as: slowing down at intersections, avoiding sharp turns at speed and reducing speed to accommodate dangerous conditions like wet floors. Employers should also mark speed limits clearly in the warehouse and enforce compliance through regular supervision.
Staying Aware and Avoiding Distractions
Situational awareness is a critical skill for all warehouse workers. Warehouse supervisors should constantly reinforce best practices for awareness with their workers to help them avoid collisions or other incidents. Warehouses should implement traffic management systems, such as one-way lanes or designated pedestrian walkways, to minimize conflicts between workers and power lift equipment. In addition, equipment operators should be trained to:
- Check Blind Spots: Using mirrors or cameras to see areas behind or around the equipment.
- Watch for Pedestrians: Slowing down and yielding to foot traffic in shared spaces.
- Avoid Hazard Zones: Staying clear of areas with uneven terrain, low ceilings, or narrow passages.
Distractions can also significantly impair an operator’s ability to control power lift equipment safely. It is common to prohibit the use of phones or headphones during equipment operation. In addition, workers should completely halt equipment when communicating or interacting with coworkers. Employers should enforce a zero-tolerance policy for distracted operation and educate workers on the dangers of inattention.
Preparing for Emergencies
Despite all precautions, accidents can still occur. Workers must be trained to respond quickly and effectively in emergency situations. Key preparedness steps include:
- Shutting Down Equipment: Knowing how to safely power down machines in case of malfunction.
- Using Fire Extinguishers: Being familiar with the location and use of fire suppression tools.
- Reporting Incidents: Documenting accidents or near misses to supervisors and safety teams quickly and with complete information.
Regularly conducting emergency drills helps ensure that workers are ready to act promptly and appropriately when needed.
The Role of Employers in Promoting Warehouse Equipment Safety
While individual workers bear responsibility for their actions, employers play a vital role in ensuring warehouse equipment and worker safety. Warehouse operators should take all steps possible to provide safe, high-quality lift equipment, PPE, and training materials.
Management should prioritize safety best practices. This can be done by clearly sharing and promoting safety protocols and standards. They should also enforce penalties for those who do not follow these rules. Hazard and incident reporting should be made as easy as possible so that workers can encourage participation and engagement in warehouse equipment safety practices.
Many warehouse operators are turning to digital tools on mobile devices to help institute best practices for equipment safety. Digital tools, like Driveroo and ROO.AI, can provide easy access to safety training and faster, simplified inspections for equipment pre-operation checks and maintenance. Digital tools also facilitate hazard and incident reporting, walking workers step-by-step through the reporting process and making information available immediately for management to take corrective actions.
Operating power lift equipment in a warehouse is a high-stakes responsibility that requires vigilance, training, and adherence to established protocols. By following best practices for safely operating power lift equipment, warehouse workers can minimize risks and ensure a safe, efficient working environment. Employers must also support these efforts by providing the necessary tools, training, and oversight. When safety becomes a shared priority, the entire organization benefits through reduced injuries, improved morale, and enhanced productivity.